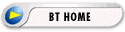

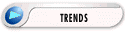
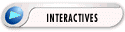
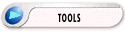
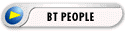
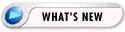
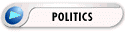
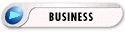
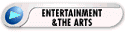
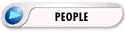
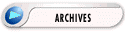
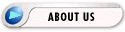 |
C O N T I N G E N C Y
Riding The Storm
Maruti has found an innovative answer to
its labour problem: get vendors to work the assembly lines.
By
Suveen K. Sinha
Last
month, Heavy Industries and Public Enterprises Minister Manohar Joshi sent
one of his bureaucrats to Maruti Udyog's plant in Gurgaon. The minister
took the unusual step because he was not ready to believe what he had just
heard: that the car maker's production had been steadily rising inspite of
the unionised workers staying away from work. But the bureaucrat confirmed
what the minister had found hard to believe. Maruti's average daily
production in November stood at 1,319 units, against 1,205 in the
pre-strike days of April-September.
Joshi's incredulity is understandable. The
unions, which account for 4,444 employees from Maruti's total workforce of
5,730, went on strike in October 2000. Expectedly, the production slumped
to an abysmal 299 on October 12. That was when CEO Jagdish Khattar-who
once, as a Tea Board member stationed in UK in the early 1980s, personally
carried tea samples around exhibitions-decided to implement some of his
innovative ideas. Today, the result is there for all to see: a lot of
unfamiliar faces working the lines at Maruti's Gurgaon plant. They are
workers borrowed from some Maruti vendors. Thus, the air-conditioning
station is manned by people from Subros, the fuel tank line by those from
Remark Auto, and so on. ''They know their work. All they needed was a
day's training,'' says Khattar, not trying to hide his glee.
Secondly, old apprentices-Maruti takes on
1,200 of those every year-have been called back. They are happy to return,
since Maruti is paying them Rs 5,000 a month against an average of Rs
2,500 they earned in their previous jobs. As Khattar went about scavenging
for workforce, employees from various departments, including engineering
and even quality control, were put on the shop floor. And about a
dozen-odd non-production people (including drivers) who are sent to
Suzuki's facilities in Japan every year as part of a 120-strong
contingent, were called upon to put their learning to use.
Even as the unions are threatening to
disrupt the new arrangement-they were earlier dismissing the production
figures as a mere clearing of inventory-Khattar is drawing kudos for his
nifty solution. Former Daewoo Motors India Chairman S.G. Awasthi feels
that Khattar's approach is reasonable and fair. ''The management should
never submit to exploitation by unions. Secondly, these measures will
build relations with vendors beyond the regular operations,'' says he.
Khattar is happy because, apart from the
rise in absolute numbers, there has been a rise in productivity. For
instance, the production was 1,432 units on the fifth of December, with
only 4,035 workers working 1.4 shifts (11 hours) against the two shifts
(16 hours) in pre-strike days. Besides, the average daily line-run without
component, average daily hold-up, and the downtime for the plant (all
measures of inefficiency) have gone down, while the quality index has gone
up. ''They (the make-shift workforce) must be doing a good job,'' says
Khattar. The arrangement may also result in some reduction in the
company's wage costs (regular employees earn Rs 23,000 a month) if Khattar
walks his talk: ''No way. No work, no pay.'' Clearly, it's an iron hand
that now drives Maruti.
|