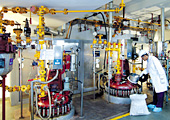 |
Specialty chemicals account for only $9
billion of the $36-billion chemicals industry in India |
Want to see
R&D-driven manufacturing in action? Drop by at Jubilant Organosys'
facility at Gajraula in Uttar Pradesh. One of the two specialty
chemicals factories that the Delhi-based company runs, it's a
live example of how Indian manufacturers are taking Chinese rivals,
who have a dominant share of global exports, head on.
About two years ago, Jubilant's Head of specialty chemicals
business, S.N. Singh, was a worried man. One of their top-selling
specialty chemicals had suddenly come under fire from the Chinese.
Compared to Jubilant's sticker price of Rs 2,500 per kg, some
Chinese manufacturers had started selling the same product at
less than half the price (Rs 1,200 per kg, to be precise). Threatened
with a loss of market, Jubilant's chemists went back to their
vats and beakers to find ways to cut production costs. After three
months of R&D, they came up with a manufacturing process that
allowed them to sell the same specialty chemical at a price lower
than that of the Chinese. "This business is knowledge-driven,
and you have to continuously innovate to stay ahead of your competitors,"
quips Jubilant's Singh.
The chemicals business can be broadly divided into three categories:
Basic, specialty and high-end. Specialty chemicals, which go into
things like adhesive sealants and plastic additives, are produced
in smaller quantities compared to bulk chemicals, and demand a
high degree of technical input and R&D.
SECTORAL SNAPSHOT |
»
India's specialty chemicals industry is expected
to grow at a CAGR of 15 per cent compared to global industry
projected rate of 7.5 per cent
» In 2007,
the Indian specialty chemicals market will be worth $11 billion
(Rs 50,600 crore), including $3 billion (Rs 13,800 crore)
of imports
» Indian
specialty chemical exports are expected to touch $13 billion
(Rs 59,800 crore) in 2013 from $4 billion in 2007, and $33
billion in 2018 |
Therefore, while India's chemicals industry is $36-billion (Rs
1,65,600-crore) big, specialty chemicals account for only $9 billion
(Rs 41,400 crore). But like in pharmaceuticals, global industry
dynamics are changing, and the big players are expected to either
shift manufacturing to low-cost countries or buy from them. The
reasons are all familiar: Profits of manufacturers in the West
are under pressure; a lot of user industries are shifting factories
to Asia, forcing their suppliers to tag along; and, more importantly,
manufacturers in countries like India and China have matured rapidly
in terms of their competence. In India's case, a better intellectual
property regime starting 2005 is an added attraction for manufacturers
abroad to outsource production.
That said, the industry still has a long way to go. India has
traditionally had a fragmented chemicals industry and that continues
to be a competitive hurdle. "Even though India had a significant
domestic market for some constituents of chemical industry like
dyestuffs, it never got translated into economies of scale in
manufacturing," points out Sunil Lalbhai, MD & CEO of
Atul, an Atul-based (Valsad district, Gujarat) manufacturer of
specialty chemicals. "As a result, China has beaten India
in this game." Besides, within the value chain, there are
inverted duty structures for intermediates and finished goods,
leading to high input costs for some producers, who are then rendered
unviable even if they are efficient. Power apart, "the rigid
labour laws are making it very difficult to restructure businesses
and this has led to increased inefficiencies", notes Lalbhai.
Jubilant's Singh points out that even 'softer' issues such as
environment, health and safety (EHS) have become very important.
Traditionally, Indian companies have paid little attention to
EHS, but these days it is considered a hygiene factor. Just like
customers abroad frown upon use of child labour, they shun manufacturers
who aren't environment- and labour-friendly. "The concept
looks at a business' impact on the triple bottom line of economy,
environment and society," says Singh.
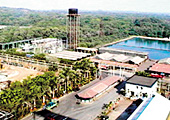 |
Issues such as environment, health and safety
have assumed importance for Indian specialty chemical
makers |
One of the reasons why manufacturers in India are competitive
is the large pool of engineers and chemists. At least in the case
of low-volume, batch-processed chemicals, that is a big advantage.
Companies, however, fear that to maintain India's edge, the country
needs to churn out larger number of skilled and unskilled workers.
Among the solutions, they say, is to enhance the collaboration
between industry and academia for innovation, and to step up supply
of skilled workers. "The way things are moving, it is expected
there will be an acute shortage of talent within five years,"
says Singh. If manpower costs go up without any significant gain
in process or product breakthroughs, then competitiveness of Indian
manufacturing will suffer across the board.
No wonder, people like Lalbhai of Atul say that the path ahead
for this industry has to be different from the one India has followed
so far. To build global competitiveness, he says, India requires
a multi-pronged approach and a comprehensive strategy to address
crucial aspects of infrastructure, technology and investments.
"First, we must encourage and enable existing investments
to restructure and become competitive," says Lalbhai. "This
may mean an exit from one location or from one product line to
another.
However, rigid labour laws prevent this logical step towards
competitiveness. Lalbhai's lament may sound all too familiar,
but it carries an important message: When you are fighting in
the cut-throat global markets, every millimetre of strategic elbow
room counts.
|