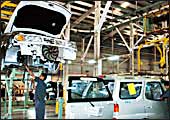 |
MEAN MACHINE: For those sceptical of Tata
Motors' new global thrust, a visit to its 1,200-acre Pune plant
can be eye-opening |
In
the fifth and final shop at K-block, the 200-odd acre passenger
car making plant of Tata Motors, there's a spanking new automobile
rolling out every 98-100 seconds-Tata Indicas, a few Indigo sedans,
and a sprinkling of the soon-to-be-launched Marina station wagons.
This is the trim and assembly shop where workers armed with pneumatic
and hydraulic nut runners are fitting the engine, front drives,
radiator and into the shell of the car.
A worker fits an engine in 90 seconds flat,
whilst moving on a trolley. The day's target is 540 cars in two
shifts. The first shift began at 6.30 am, and will end at 3.30 pm-the
first car to hit the ground running at 6.30 am is kept before an
idol of Lord Ganesh at the entrance of the assembly shop. It's 1
pm now: 195 cars have rolled out so far. The indicator reveals that
12 minutes have been lost. But there's little trace of worry on
the shopfloor. The day's target will be met. Engines and doors continue
to move around-it's difficult to imagine, but all the movements
are synchronised and flexible. Don't worry. An Indica door won't
latch itself onto an Indigo body. When it's time to exit the assembly
shop 195 has moved on to 198.
An Indica on the road may not warrant a second
glance-not five years after launch anyways-but a visit to the sprawling
manufacturing facilities of Tata Motors in Pune's Pimpri-Chinchwad
region offers you little choice but to view the Indica as an engineering
marvel. There are officials who will ensure you never in your lifetime
forget that Mercedes cars are painted in the Tata workshop; or that
no human touches a Tata car in the press shop, weld shop and the
paint show. They'll also tell you the Indica was the first time
that the Tatas were making a monocoque vehicle (all the others are
body-on-frame), and that for a plant that started making 40 cars
a day to be doing 500 (and in a few months 750) is nothing short
of remarkable.
As is indeed the entire Tata Motors plant,
which includes the commercial vehicles factories and foundries,
besides the passenger car division, spread over 1,200 acres, with
just the training centre and the production and engineering centre
(or the toolroom, where dyes, fixtures and patterns are made) common
to both heavy vehicles and cars. A visit to the training centre
in many ways sets you up to take in the entire plant. Here, 100
apprentices are put through the paces, and 20 per cent of them are
absorbed at the end of a three-year course (the 100 are selected
from 10,000 applications for a three-year course during which they're
trained in the 19 trades required in the automobile industry).
|
RUGGED AND RELIABLE
|
»
There's a car rolling out every 98-100 seconds
» Currently
making 540 cars in two shifts. Will soon go up to 750, and then
1,000
» Mercedes
cars are painted in the Tata paint shop
» Value-addition
by vendors will soon touch 75-77 per cent
» A
whole range of CVs, right from 1 tonne to upwards of 35 tonnes,
in various stages of launch |
Cut-sections of Tata Motors' entire range of
cars and trucks lie scattered across the training centre. In one
corner, a group of apprentices is coming to grips with CRDI technology
(Common Rail Direct Injection-watch out for a CRDI version of the
Indigo Diesel), and another bunch is working on a battery-operated
Indica. On another side, a 1926 Rolls-Royce that was brought in
scrap condition 12 years ago, and which has since been restored
by the apprentices, is displayed in its resplendent glory.
Each visit to the various sections of the Tata
Motors' plant is a story in itself. Should you be focusing on the
new Sumo Victas, which roll out every seven minutes, with 17 "major"
changes (bucket seats, sturdier suspensions, power steering and
windows, a 2.1 litre turbo-charged water-cooled engine et al)? Or
should you hammer out a few paras on the one-time order from the
Algerian police for 1,500 Safaris-left-hand drive, green and white,
4x4 drive, with siren and lights perched on top. There are a few
Safaris branded Ex 2 that are going to Spain too.
Perhaps the testing area-the "torture
track"-will make better copy: There's the crash-test facility,
the track for durability testing, the water-wading and gradient
tests, Belgian bumps, potholes, and an area where engine emissions
are tested. Prototypes of the various vehicles are dragged to the
torture-there's a Marina prototype that's just been, well, tortured,
and a seemingly rattled Leyland bus too, cools its heels (the competitor's
presence is a benchmarking imperative). After the torment, the vehicles
are taken to the engineering research centre (ERC), dismantled,
examined, and modifications, if necessary, are suggested.
From the design studios of the ERC, the nerve
centre for new Tata vehicles, you can expect many more Indica variants,
a new Indica platform and the much-touted Rs 1-lakh car to zoom
off the drawing boards. Most of the activity within the ERC-where
you're most likely to find Dr V. Sumantran, the former General Motors
pointman, brainstorming with a bunch of young designers-is aimed
at bridging the quality chasm that exists between Tata's products,
specially CVs, and global majors. After all, if Tata Motors wants
to go global it can't be as simple as a mere pr pitch. "Our
vehicles are rugged, robust, but lack aesthetics and finish. So
the products get discounted. So we are investing in these facilities,"
points out P.M. Telang, Senior Vice President (Operations).
Most of the activity at the Tata plant, and
particularly within the ERC, is geared towards erasing one very
unenviable reputation the company has earned over the years: That
a Tata product is a rugged, reliable machine-but be prepared to
deal with the initial tribulations that inevitably come along with
every purchase.
|