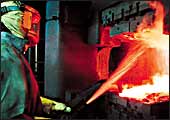 |
FORGING A WINNER: The Virtual Manufacturing
Process at Bharat Forge's Pune plant enables it to be online
with global clients like Ford, Volvo, and Daimler-Chrysler |
On
the face of it, it's as Old Economy as they come: Glowing furnaces,
overhaul-clad workers tending conveyor belts supervised by hard-hat
supervisors, the crash and shudder of heavy duty presses and through
the dust, heat and grime, neat stacks of forged steel making their
way to waiting trucks.
But peel back a layer of epidermis at Bharat
Forge's sprawling 80- acre plant at Mundhwa, Pune and what you unearth
is something completely different. What MIT-trained engineer turned
entrepreneur Baba Kalyani refers to as ''driven more by brain power
than muscle power''.
As Chairman and Managing Director, Kalyani
heads the 43-year-old engineering firm that's already the world's
second largest forging manufacturer. Today, it turns outs a capacity
of 100,000 tonnes annually, which will be doubled over the next
few years. Its appetite whetted by organic growth, Bharat Forge
recently acquired CDP, one of largest forging companies in Germany.
A peek into the first floor Engineering and
Design Centre throws more light on what Kalyani's talking about.
''It's the brain and heart of the plant,'' informs Senior Vice President,
Shyam Takale. In the harsh fluorescent light 40-odd engineers sit
peering at swirling colourful shapes on 21'' monitors, interspersed
with frantic clicks on the mouse and furious calculations.
Bharat Forge supplies crankshafts, axle beams,
steering knuckles and assorted transmission parts for auto manufacturers
across the world. Now, just how much technology can be needed to
hammer and mould a slab of steel into a flat motor part? Takale,
a US-trained engineer who's been walking shop-floors for over 15
years, steps in to provide the answers: The heart of the production
process is the ''die''-an unassuming partially hollowed out metal
block. From the kind of metal to be used to the designing to the
contours of the indentations, everything has to be got just right.
Because not only will 4,000-5,000 pieces have come off each die,
but dies often have to bear loads as staggering as 16,000 tonnes
of pressure.
LIVING WITH DIES
|
»
Makes crankshafts, axle beams, steering knuckles
and assorted transmission parts for auto majors like Daimler
Chrysler, Ford, and Volvo
» Entire
die production process is automated, and computers online with
global clients
» High-speed
machines and automated production lines have boosted productivity
» Product
development takes just two to three weeks, as against six to
eight months earlier
» Manufacturing
expenses and manpower costs reducing by the day |
Since the quality of the final forged product
is a function of the quality of the die, Bharat Forge's Virtual
Manufacturing Process-using the latest in cad/cam and modeling software-continuously
maps and monitors critical parameters like forgability, load capacity,
die deflection and stress levels. Lately the tool room has also
been integrated, which means that the entire die production process
is now automated. ''Sitting here in the control room we control
everything-accuracy levels, machine utilisation, operator efficiency,''
elaborates Takale. Furthermore, computers are online with international
clients like Ford, Volvo and Daimler-Chrysler. This means requirements,
specifications and even 3-D machine models can be swapped, making
design a continuous and iterative process.
Bharat Forge has invested Rs 630-crore in upgradations
since 1990. The improvement is visible in the tool room, where high-speed
machines have boosted productivity. Manufacturing expenses as a
percentage of income have come down from 19.6 to 16.7 per cent and
manpower costs from 6.9 to 6.1 per cent.
Product development, which earlier used to
take six-to-eight months, today takes only two-to- three weeks,
a front axle beam die, which earlier took 130 hours to make, now
only takes 13 hours. First-time success rates are as high as 98
per cent and design time has been cut down by a tenth. Accuracy
of die has been brought down to 0.05 mm (from 0.4 mm), draft angles
narrowed to half-a-degree and a glistening surface finish of 3 microns
has been achieved. And don't forget that at any point in time Bharat
Forge is juggling with inventory of 600-700 product variants ranging
from a 350-kg crankshaft manufactured for Cummins to a 50-cm transmission
part for Toyota. ''There's so much of demand, we often find it difficult
to keep up,'' is how Kalyani sums it up.
|