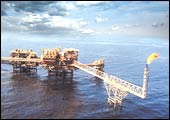 |
Rigs like this can remotely control up to 15
unmanned platforms |
The
choppy waters of the Arabian Sea can be unnerving to the novice.
That the site is potentially a high-risk target for enemy missiles
in the event of a war with Pakistan only makes it more dangerous.
The loud rattling sound of 45,000 barrels of crude as it noisily
blunders through the pipeline to Mumbai every month could easily
make a visitor wonder if rivalries have already begun.
These are not worries for old hand Rajiv Singh, an
engineer with the Oil and Natural Gas Corporation (ONGC), as he
goes about his dawn-to-dusk work routine, analysing data pouring
in from 750 offshore wells. The wells are spread over 1,200 square
km, and make up the fabled area we all know as Bombay High. Sitting
in a control room nearly 160 kms off Mumbai on a spider-like rig
with three iron and steel arms, Singh is one of about 100 engineers
from ONGC who makes his home here for 14 days at a stretch.
Suddenly a beep on a monitor tells Singh that
the pressure of oil flowing out of a group of rigs has fallen sharply.
After some routine checks, he taps a few keys and flips a few switches.
Instantly, the meter shows the pressure of crude oil outflow from
those oil wells has dropped to zero. Singh has successfully closed
the faulty valve at six of the wells, located some 3 km away.
What's remarkable is that there isn't a soul
on those rigs. If he so wanted, Singh could even switch off the
motor or pumps that extract crude oil from the sea bottom. Tomorrow,
a team of two engineers will visit the unmanned platform the next
morning and make sure everything gets back to normal.
Unmanned rigs, controlled by microchips and
wireless, have helped ONGC achieve world-class manpower and functional
efficiencies-but only on its offshore rigs. This is just one aspect
of the wired life at the daily operations of India's main crude
oil producer. ONGC, also the largest Indian oil exploration company,
is now in the process of setting a new computer network that could
be one of India's hottest.
ONGC: FAST FACTS
|
» Number
of Oil wells 4,700 (700 offshore)
» Oil production
24.7 million tonnes*
(Total Indian demand: 80 million tonnes)
» Revenues
Rs 24,270 crore**
» Number
of employees 40,226
» Number
of PCs More than 8,000
(* in March 2002) (** March 2001) |
"Our
business is helped by knowledge"
Subir Raha, Chairman, ONGC |
The Wired Lifeline
''We are not in the knowledge business,"
says Subir Raha, Chairman and Managing Director of ONGC. "But
our business is helped by knowledge.'' He needs the network, he
adds, to help manage his 40,226 employees-the company intranet is
accessed by 700 people every day-scattered in far-flung locations
across India. He needs it to control and manage oil production,
gradually even pricing, as ONGC's output gets set to touch 24.7
million tonnes by March 2002-that meets a critical 30 per cent of
India's oil needs. The successful wireless operations offshore,
are now going to be replicated onshore.
Raha's penchant for wiring up was not particularly
easy to justify to his board though, whose approval he had to seek
before spending more than Rs 700 crore over two years on ONGC's
it infrastructure. It was certainly one of the largest it budgets
of any Indian company. But Raha, formerly with Indian Oil Corporation
(India's largest oil company), had done his homework. He was quick
to point out that ONGC was using six different computer systems
for different divisions. It was a wired mess. All of them needed
to be brought on to a common platform to ensure smooth decision
making. The benefits that would accrue from an on-tap information
process, to him, went beyond quantification.
ONGC's big spend on wiring up couldn't have
come at a more opportune time. With the dismantling of the administered
price regime from April 1, 2002, ONGC needs every efficiency it
can muster. The company will no longer continue with its one-price-fits-all
philosophy. Based on real-time data of oil production, its pricing
mechanism will vary prices between customers. And a year from now,
ONGC wants to morph into just-in-time production methods to meet
the demands of a globalising market.
''The idea was to put all the systems on the
same platform, technical and managerial,'' says A.T. Kabilan, a
mechanical engineer who has earlier served a four-year stint at
Bombay High. ''With the different systems that various departments
in ONGC have, it would not have been possible for a senior executive
to take effective decisions quickly.''
HOW WIRING UP WORKS FOR ONGC
|
»
ONGC had separate networks for HR, finance, materials
management, production and other functions, which ran independent
of each other-a wired mess.
NOW The new network will
encompass all operations of the company.
Decision-making will be instantaneous.
» A problem
or glitch on unwired onshore rigs could take up to two days
to locate. Engineers then had to establish its nature.
NOW The new network will
monitor oil flow real time, as on the unmanned wired offshore
rigs. Less wastage, lower costs.
» Pricing
wasn't really a problem for ONGC's accounting system-one price
fitted all over the last few decades.
NOW With the dismantling
of the administered price regime from April 1, ONGC-aided by
real-time data of crude oil production-will vary prices between
customers.
» Managing
employees in locations in the remotest corners of India was
a nightmare. Communications could reach employees after nearly
15 days.
NOW The company intranet,
accessed by nearly 700 employees every day, has made communication
instantaneous. |
Some 160 kms off the coast of Mumbai, there
are 140 unmanned platforms and another 14 manned platforms. Each
of the 140 unmanned platforms have 10-12 oil wells around them,
which are wirelessly connected to the control room at the manned
platform, with nearly 100 personnel working at any point of time.
The control room monitors the flow of oil 365X7 through the 203-km
long pipe that ferries the crude oil inland. After making landfall,
the oil pipeline is diverted to Uran in Maharashtra, the gas to
Hazira in Gujarat. To ensure that the wireless connectivity between
the platforms, the control room, the pipeline, and the plants never
goes down, ONGC has satellite back-up, in case the radio link goes
down.
One million tonnes of oil can cost nearly Rs
350 crore at the current prices. So it's very important for the
public sector monolith to minimise wastage. Every fault is a few
crores down the drain. ONGC's system can pinpoint faults, localise
them, then direct engineers for repairs. Tackling a fault as soon
as it is detected not only saves oil but also minimises damage caused
to a rig.
The only way these critical unmanned platforms
can be effectively managed is through a 24X7 information network.
That is another reason why all critical information about the functioning
of the oil wells around a rig is available at the tap of a button.
The platform is just large enough for a helicopter. A team of two
engineers visits nearly three such platforms each day to physically
inspect that all is well.
The control room at the manned platform has
a team of 10 engineers with varied specialisations. They could remain
offshore in Mumbai, but a one-way 45-minute helicopter ride to Bombay
High costs about Rs 24,000 per head.
Another great challenge in offshore drilling
is to keep the machinery in running condition. Again, the network
steps in. Sitting at the control room and monitoring oil extraction
in 700 wells, controllers like Singh can explore the drilling system-much
like a physician runs a stethoscope over a patient-and see how turbines,
motors, and pumps are working. But while over 70 per cent of daily
operations are managed through the wired system, the onshore figure
is half of that.
Much of the efficiencies ONGC wants to bring
about will come from wiring onshore wells. From the lessons learned
from the wireless offshore network, the company hopes that the regular
maintenance visits of its engineers to its 4,000-odd wells spread
across India will reduce dramatically.
Oil can be a slippery-and costly-business.
One small mistake and the cost of drilling for each well, estimated
at between Rs 50-100 crore, can go down the drain. Precision of
decisions, and information, is the key to efficient operation.
If countrywide wiring up works, leakages can
be monitored instantly. And it will be possible for one control
room to oversee many more wells onshore than is done offshore. The
longer the delays, the longer the stoppage in production of black
gold-something India can ill-afford with the war clouds that now
gather routinely on our horizons.
|